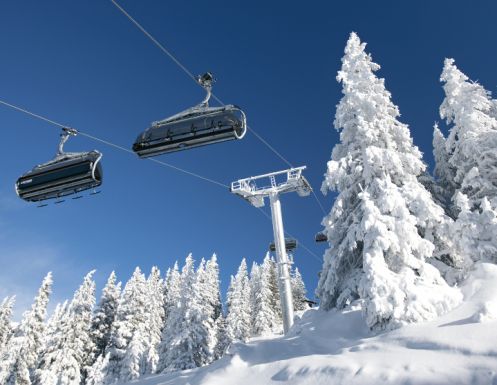
Per gli sciatori e gli amanti della montagna, Leitner è un marchio molto noto. I suoi impianti, infatti, sono il complemento fondamentale di ogni sport invernale, migliorando l’attrattività delle strutture ricreative grazie a seggiovie e cabinovie ad agganciamento automatico, funicolari, funivie, ascensori inclinati e skilift confortevoli e sicuri.
Data la tipologia di prodotto, il modello di business è molto complesso: come produttore Leitner necessita di materie prime, lavorati e semilavorati che, tra lamiere e profilati in acciaio, funi, sistemi di controllo elettronico, riduttori, freni, sedute e parti elettrotecniche, comporta la gestione di oltre 900 fornitori diversi. Tra i provider, infatti, c’è persino BMW che fornisce sedute in pelle riscaldate per cabine superlusso, dotate di frigo bar e display interattivi per l’infotainment dei viaggiatori.
Il processo di produzione include fasi diverse, dal taglio alla saldatura, dalle lavorazioni meccaniche a verniciatura e montaggi finali, secondo i vari modelli a catalogo e relative varianti e personalizzazioni. Una volta terminati i sottogruppi degli impianti in base alle varie configurazioni dell’ordine, la distribuzione coinvolge poi una rete di 110 trasportatori. Si tratta di referenti diversi, che coprono le attività di trasporto navale e stradale in ambienti anche molto difficili: in montagna, infatti, servono mezzi speciali, a 4 ruote motrici, per trasportare i sottogruppi degli impianti per il montaggio finale, realizzato in loco.
Ottimizzare i processi di trasporto
Le maggiori sfide per Leitner sono a livello produttivo ma a anche a livello logistico, con una gestione concretamente complessa: ogni ordine include tantissimi codici di prodotto e va

accompagnato dalle specifiche di montaggio e relativi disegni aggiornati. Sia outbound che inbound, l’organizzazione deve risolvere una pluralità di indirizzi di presa (1100) e di consegna (1300) su una movimentazione che comprende una media di 18.500 prese l’anno. Nel 2008, la volontà di ottimizzare meglio la Supply Chain ha spinto la società a reingegnerizzare i processi, avviando un progetto di implementazione SAP a livello di gruppo. Con l’occasione, la direzione puntava a introdurre anche un sistema di Transport Management System (TMS) che potesse garantire la gestione completa degli ordini di trasporto e la gestione documentale di ordini e conferme d’ordine, includendo la parte più organizzativa del ritiro dei materiali presso i fornitori.
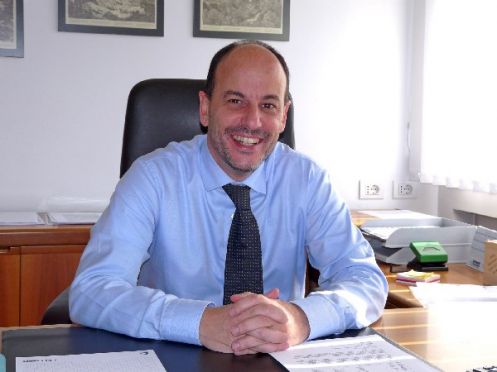
«Cercavamo un sistema integrabile con SAP ma anche di facile utilizzo, performante e multilingua – spiega Marco Goss, Chief Supply Chain Officer di Leitner -. Tra i requisiti della soluzione, avevamo necessità che il partner fosse affidabile, in modo da garantire lo sviluppo dell’applicazione e la sua sostenibilità negli anni. Abbiamo scelto la soluzione proposta da Tesisquare e nel 2009 abbiamo iniziato a implementare il sistema: TMS si è dimostrato subito molto valido, non solo portando maggiore efficienza e precisione nei processi, ma anche velocizzando tutte le procedure associate alla logistica e alla movimentazione dei prodotti, garantendoci una riduzione dei costi di trasporto tra il 5 e il 10% ma anche una riduzione delle ore uomo necessarie di un 15%».
Una supply chain ad alto tasso di collaborazione
La soluzione ha incrementato la visibilità ma anche la collaborazione tra tutti i referenti della Supply Chain, ovvero fornitori, trasportatori e produttori, introducendo elementi di automazione e di semplificazione che hanno innalzato la qualità delle attività, abbattendo i tempi e ottimizzando le risorse.
Oggi gli ordini vengono inviati automaticamente ai trasportatori, riducendo di conseguenza il numero di mail e telefonate. La soluzione adottata ha consentito una reportistica avanzata che ha introdotto nel Gruppo una tracciabilità dei trasporti e dei prezzi espressa attraverso indicatori importanti (KPI). Il Gruppo può gestire richieste di trasporto anche su più stabilimenti e su diverse nazioni, organizzando i viaggi tramite un’unica interfaccia on line, il che consente di ottimizzare i carichi riuscendo a migliorare la saturazione dei mezzi, favorendo così una razionalizzazione delle attività e dei consumi (con il vantaggio di ridurre l’impatto ambientale della logistica).
Tra i vantaggi di TMS va aggiunta anche la possibilità di avere un numero identificativo unico rispetto alla richiesta di trasporto, per consentire il riconoscimento immediato in fase di ritiro dai fornitori o dai clienti, velocizzando ulteriormente il processo.
«La possibilità di elaborare statistiche avanzate, con accesso al database aggiornato – ha proseguito Goss – ci permette di analizzare approfonditamente le variabili associate ai trasporti come il livello di saturazione, il calcolo dei pesi medi o la valutazione dei trasporti diretti/indiretti, permettendoci di controllare meglio i costi. Non solo: la sistematizzazione dei processi, grazie all’invio automatico degli Ordini di Trasporto ai trasportatori, ha velocizzato i processi di consegna, permettendoci di gestire i listini in modo automatizzato con modalità di aggiornamento decisamente semplificate. Un altro plus è la possibilità di effettuare il controllo e la conferma delle fatture dei trasportatori che vengono poi automaticamente caricate sull’ERP, con un’assegnazione corretta dei costi relativi ai vari progetti. I risparmi che abbiamo ottenuto con questa soluzione si attestano tra il 5 e il 10%, con una riduzione delle ore del personale dedicate all’attività di un 15%».
Dal document management alla conservazione sostitutiva in un’unica soluzione di continuità
Nel 2012 Leitner decide di estendere l’ingegnerizzazione anche alla parte di gestione dei fornitori, aggiungendo una soluzione di Vendor management, integrato a SAP e al sistema di TMS.
Nel 2014 inizia l’avviamento prima al Gruppo Leitner e poi al Gruppo Poma, la divisione francese del Gruppo. «Oggi, tramite un unico portale – conclude Goss – possiamo inviare automaticamente dal nostro sistema ERP al nostro sistema di SCM ordini di acquisto ai fornitori e documenti correlati relativi a specifiche e disegni aggiornati. In questo modo possiamo gestire automaticamente le conferme d’ordine, con aggiornamenti e avvisi di spedizione con una estrema precisione rispetto alla disponibilità delle merci in produzione, proprio grazie alla migliorata puntualità dei fornitori. Il processo automatizzato include anche la gestione delle richieste di ritiro da parte dei fornitori come input integrato tra i due sistemi. A livello di valutazione delle performance, siamo passati dall’82% al 90% di puntualità, guadagnando ben 8 punti percentuali in più. Insomma, siamo passati da un pregresso basato su una quantità di fogli Excel a un sistema evoluto, integrato, digitalizzato e ad altissime prestazioni».
Grazie a SCM il Gruppo ha introdotto una soluzione che dal document management alla conservazione sostitutiva, ha dematerializzato i processi attraverso un’unica soluzione di continuità. Gestione dei workflow, notifiche e alerting, questionari dinamici, dashboard e KPI sono tutti elementi di supporto al Gruppo attraverso moduli integrati e personalizzabili.
I risultati di questa digitalizzazione spinta di tutti i processi gestionali, oltre a garantire l’affidabilità dei dati e la massima trasparenza informativa, ha avuto un impatto positivo sull’intera supply chain del Gruppo, migliorando non soltanto le performance dei trasportatori ma anche la logistica interna dei cantieri perché ad oggi le consegne sono tutte registrate e non ci sono motivi di contestazione grazie a un livello di controllo relativo sia all’approvazione degli ordini che ai documenti di trasporto con un tracciamento anche della data di consegna. Il tutto messo a sistema.
*****Leitner, funivie non solo per l’alta quota*****
L’azienda altoatesina, con sede a Vipiteno, è stata fondata nel 1888: nel corso degli anni, la qualità della progettazione e della produzione hanno portato l’azienda a diversificare l’offerta e a definire un modello di business che le ha permesso di varcare i confini nazionali, diventando un gruppo a livello mondiale, con oltre 3.000 dipendenti e un fatturato di gruppo che nel 2014 ha superato i 700 milioni di euro.
Oggi, infatti, Leitner è parte di una realtà imprenditoriale multinazionale specializzata in tecnologie funiviarie (Leitner e Poma), impianti per l’innevamento artificiale (Demaclenko), veicoli battipista e veicoli cingolati multiuso (Prinoth) e impianti eolici (Leitwind).
Le soluzioni proposte non sono più finalizzate esclusivamente all’alta quota: sia in Italia che all’estero, infatti, diverse città hanno risolto l’equazione economia/ecologia legata ai problemi del traffico urbano, adottando gli impianti a fune (aeree e su rotaia) per il trasporto pubblico del Gruppo: da Perugia a Rio de Janeiro, dalla Turchia alla Colombia.
Attualmente il Gruppo conta 70 filiali, 127 punti vendita e assistenza e 8 stabilimenti produttivi dislocati in Italia, Austria, Slovacchia, Francia, Nord America e India.