Le medie imprese credono in Industria 4.0 e AI (intelligenza artificiale), in particolare quelle del Nord-Est. Lo dimostrano i casi di Breton, Brovedani, Friul Intagli Industries, e LimaCorporate, presentati dai loro stessi manager in un evento di Microsoft e del partner beanTech. Vediamoli più in dettaglio.
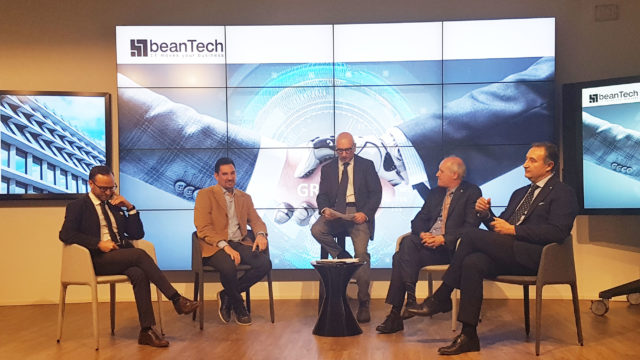
Indice degli argomenti
Breton: monitoraggio delle macchine su smartphone
Breton SpA è un’azienda trevigiana a conduzione familiare che produce macchine utensili per la lavorazione della pietra e dei metalli, con 7 filiali estere, 900 dipendenti e fatturato di 200 milioni di euro, di cui quasi la metà all’estero.
Ha avviato alcuni anni fa il programma “Breton Innoway”, per introdurre un modello di Lean Production per la gestione dell’ordine cliente e lo sviluppo di nuovi prodotti. In quest’ambito ha sviluppato Sentinel, soluzione basata su Azure e Power BI di Microsoft per il monitoraggio in tempo reale delle macchine utensili da pc, tablet e smartphone.
«È un “ponte” tra gestione della produzione (MES) e livello macchina: raccoglie ed elabora dati dal campo, e per le imprese meno strutturate può essere il primo passo verso Industria 4.0. I benefici vengono trasferiti anche ai nostri clienti: miglior visibilità sulla produzione, incremento dell’efficienza (anche energetica) dei processi e della produttività degli impianti, riduzione dei fermi macchina, ottimizzazione della manutenzione ordinaria, e implementazione di quella predittiva», ha spiegato Enrico Favaro, CTO di Breton.
Il prossimo passo è introdurre tecnologie di Machine Learning e AI anche nei processi di lavorazione della pietra, per affrontare l’enorme variabilità delle caratteristiche fisico-chimiche del materiale, che richiede forti personalizzazioni per ogni lavorazione. «Sarà la macchina stessa a consigliare all’operatore le azioni più adatte in base all’analisi dei dati raccolti sul campo».
Brovedani: controllo qualità personalizzato sul singolo pezzo
Brovedani Group, produttore di componenti automotive (tra i clienti ha Bosch, Continental, Magneti Marelli, Eaton), ha sede a Pordenone, oltre 1000 dipendenti, e fattura circa 130 milioni di euro.
Dopo una prima fase di connessione completa delle macchine e adeguamento dei sistemi gestionali, in Italia e all’estero («queste macchine devono durare 15 anni, è un investimento che dovevamo fare subito», ha spiegato Sergio Barel, CEO di Brovedani Group), l’azienda ha avviato un piano di trasformazione digitale.
Il primo passo è stato un sistema proprietario di controllo dimensionale e qualità dei pezzi prodotti, sviluppato da beanTech su piattaforma Microsoft Azure e Power BI. Il sistema si interfaccia con l’automazione di impianto, scambiando dati con i sistemi MES e ERP, e permette di monitorare il 100% della produzione, con accuratezza delle misurazioni nell’ordine del micron.
«Anche gli operatori meno esperti possono sviluppare da soli, di volta in volta, le verifiche dimensionali e di qualità su parametri personalizzati in base alle esigenze dei diversi clienti», spiega Barel. «L’automazione avanzata e la business intelligence permettono controlli qualità fino al singolo pezzo, efficientamento del processo produttivo, riduzione degli scarti, monitoraggio continuo dei macchinari, ma anche personalizzazione del prodotto in un’ottica collaborativa con i clienti».
Nei piani futuri c’è l’integrazione di funzionalità AI per potenziare ulteriormente le capacità dell’operatore, e lo sfruttamento dei miliardi di dati raccolti per analisi predittive a fini di manutenzione, controllo qualità e correzione automatica dei processi. «Stimiamo benefici potenziali di produttività dell’ordine del 10%».
Friul Intagli, risparmi di 50mila euro anno con il nuovo reparto digitalizzato
Friul Intagli Industries SpA, con sede a Pordenone, produce componenti per mobili (900mila pezzi all’anno), con 2000 dipendenti e fatturato di oltre 500 milioni di euro al 2017.
«Abbiamo clienti come Ikea, Castorama e Walmart, che ci pagano un premio di prezzo per la qualità, ma anche una forte concorrenza. La qualità quindi deve restare altissima, ma comunque dobbiamo ridurre i costi: per questo abbiamo investito in un nuovo impianto produttivo, dotandolo – grazie al Piano Industria 4.0 – di una “spina dorsale digitale”. Raccogliamo dati da tutte le macchine ma li “rimandiamo” velocemente in fabbrica per governare gli shuttle, proporre ricette produttive, spiegare inefficienze», spiega Carlo Casetta, ICT Manager di Friul Intagli.
L’obiettivo era connettere tra loro le macchine e il sistema gestionale di produzione (MES), per automatizzare il controllo del prodotto in lavorazione, e del funzionamento dell’impianto; e misurare i consumi d’energia in linea con l’obbligo di legge per le imprese energivore. Facendo leva su tecnologie Microsoft, e in particolare su Windows 10 IoT Enterprise, beanTech ha sviluppato per Friul Intagli un Data Exchange framework, cioè un’infrastruttura hardware e software per inviare informazioni di produzione alla linea, monitorare lo stato delle macchine, storicizzare i dati produttivi, collegare i macchinari per realizzare movimentazioni automatiche.
«Grazie a questa soluzione, a regime stimiamo un risparmio del reparto produttivo di circa 50.000 euro/anno. L’idea ora è espandere il sistema anche alle linee di produzione preesistenti, e poi andare oltre, integrando Machine Learning e AI per un’analisi automatizzata più spinta dei dati a fini di controllo qualità in tempo reale, sulla linea, ed efficiente uso delle risorse». Un altro progetto pilota in corso riguarda la realtà aumentata, con uso del visore Microsoft HoloLens per interventi di riparazione, con possibilità di scalare al produttore della macchina in caso di problemi seri, dimezzando i tempi di ripristino della linea.
LimaCorporate, Demand Planning “Lean” e digitale
Infine c’è il caso di LimaCorporate, anch’essa friulana e specializzata in soluzioni ortopediche e impianti di produzione additiva (stampa 3D) nel settore sanitario, citata tra l’altro da BCG come caso d’eccellenza del Made in Italy durante la crisi economica del 2008.
Nel 2017 ha superato 200 milioni di euro di fatturato, con 900 dipendenti in 24 paesi. «Nel settore biomedicale, fortemente regolamentato, è fondamentale pianificare attentamente le decisioni di lungo periodo senza rinunciare all’agilità. Il nostro approccio a industria 4.0 è partito dalla necessità di risolvere la seria difficoltà di bilanciare il volume di produzione rispetto alla domanda», spiega Manuel Clama, Head of Corporate IT di LimaCorporate.
Da qui è partito il progetto, basato su Microsoft Azure e Power BI, e sul supporto di beanTech, per sviluppare una soluzione “Lean” di Demand Planning basata su algoritmi matematico-statistici per l’analisi dei dati storici e la previsione della domanda, un portale web per la rete commerciale, e uno strumento di visualizzazione e gestione dei dati aggregati. «Abbiamo migliorato l’accuratezza delle previsioni del 15-20%, e ridotto tempi di consegna e giacenze delle scorte, con benefici anche per gli ospedali nostri clienti, che possono pianificare meglio gli interventi».
Ora l’idea è estendere l’approccio Lean ad altre aree, come pianificazione di budget e forecast sulle vendite, «mentre in ambito Industria 4.0 stiamo valutando progetti basati anche su Realtà Mista e AI. Uno riguarda la formazione e supporto ai chirurghi tramite Microsoft HoloLens. Un altro l’uso dell’AI per il controllo visivo di qualità dei nostri prodotti, con analisi di milioni di fotogrammi in tempo reale tramite chatbot».