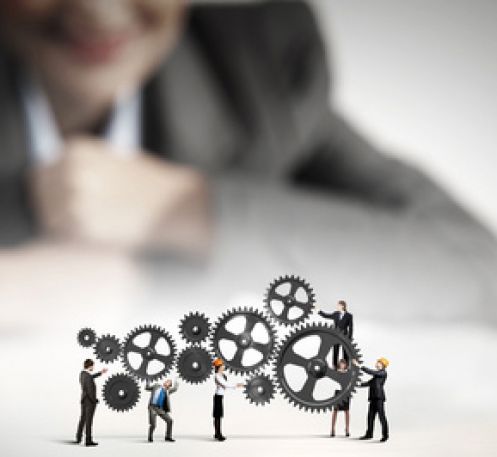
Introdotte negli anni ’70 e ’80 a partire dal Giappone e da realtà estremamente innovative come Toyota, le metodologie di gestione della qualità nella produzione, e in generale in azienda, sono state sistematizzate dal guru giapponese Masaaki Imai, che ha inventato a questo scopo il termine “kaizen”, che in giapponese significa “cambiamento in meglio”.
Il concetto di kaizen, in cui Imai ha integrato le tecniche del “Toyota Production System”, e poi Just-in-time, TQM e TPM, e i principi del Lean Management, ha preso piede negli anni anche in Italia, diffondendosi capillarmente nelle grandi aziende, ma in realtà di tutte le dimensioni, anche molto piccole, che ottengono tipicamente benefici come aumenti della produttività, e riduzioni dei difetti sul prodotto finito e del working capital (scorte e capitale circolante), nonché vantaggi più specifici delle linee di produzione, come diminuzioni del tempo di attrezzaggio macchine, del lead time, degli spazi occupati dai materiali.
Recentemente Imai è stato in Italia per presentare l’ultima edizione del suo libro, “Gemba Kaizen. Un approccio operativo alle strategie del miglioramento continuo”. La prima uscì 30 anni fa e fu un importante contributo alla diffusione del Kaizen nelle imprese occidentali. In questa Imai spiega i principi del Kaizen 2.0, l’estensione dei metodi e tecniche del miglioramento continuo all’intera organizzazione, dal nucleo originario produzione/supply chain fino allo sviluppo di nuovi mercati, prodotti e modelli di business.
Ed è anche il primo libro in cui il guru del management giapponese parla anche di casi di aziende italiane, per la precisione otto realtà che hanno fatto del kaizen uno strumento di gestione quotidiana e di miglioramento continuo in tutti i processi. Tra queste ci sono grandi realtà come Acqua Minerale San Benedetto, Carpigiani, Comer Industries, Geox e Pomini, ma anche PMI come le venete Alf Group (arredamento), Esmach (panificazione) e Rossimoda (calzature di lusso). E alle PMI italiane Imai ha dedicato considerazioni molto positive nella lectio magistralis tenuta qualche settimana fa a Bologna in occasione appunto della presentazione del libro davanti a oltre 250 imprenditori e manager in un evento organizzato da Kaizen Institute Italia.
«Kaizen incontra un grande interesse da parte delle piccole e medie imprese – ha detto Masaaki Imai – perché una volta che il proprietario decide di intraprendere Kaizen, questo diventa il modo più facile per migliorare la performance, la competitività, la qualità dei servizi. Sono stato molto impressionato dalla disciplina e dal modo in cui le persone lavorano. Da questo punto di vista posso ritenere le PMI tra i migliori casi che abbia visto, e non solo in Italia».
Scendendo più in dettaglio sui casi di PMI italiane trattati da Imai, in Alf Group, al confine tra le provincie di Treviso e Pordenone, da 50 anni produce mobili in legno, il Kaizen è arrivato nel 2009, e il percorso è tuttora in corso con tre progetti principali. Il primo riguarda Alf Uno, un sistema di produzione totalmente integrato – realizzato riorganizzando le linee di produzione e i flussi di materiale – che gestisce il ciclo completo dall’ordine alla consegna, e riduce i tempi di lavorazione (per la produzione di un pannello, per esempio, il tempo totale di permanenza in linea è stato dimezzato), e azzera il magazzino dei semilavorati. Il secondo è legato allo sviluppo su nuovi mercati, e il terzo si focalizza sul coinvolgimento della rete vendita esterna all’azienda.
Quanto a Esmach, grazie ad un’applicazione rigorosa del metodo Kaizen 2.0, spiega Imai, l’azienda di macchinari per la panificazione, con sede a Grisignano (Vicenza), ha creato un vero e proprio nuovo modello di business per i panettieri, una “panetteria chiavi in mano” che rovescia lo standard di secoli in questo settore permettendo di cuocere il pane di giorno ed evitare così i faticosi turni notturni.
Il nuovo “format” si chiama EsmachLab e concentra, in soli 15, 25 o 35 metri quadri di spazio, a seconda della tipologia scelta, cinque macchinari-base: un generatore di lievito madre, che diventa disponibile ad ogni orario della giornata, un’impastatrice automatica a spirale, una cella di lievitazione controllata con programmatore elettronico, una macchina per il taglio e il modellamento della pasta lievitata, un forno elettrico modulare a più piani.
«EsmachLab ha fatto breccia fra i forni tradizionali solo in minima parte – scrive Imai – ma ha aperto un nuovo mercato di esercenti per i quali i prodotti da forno non rappresentano il core business, ma un’opportunità per arricchire la propria offerta commerciale».
Infine Rossimoda ha realizzato un team e uno spazio dedicato per produrre rapidamente “prototipi d’autore per le grandi firme”, arrivando così a migliorare l’intero processo di sviluppo nuovi prodotti (calzature femminili di lusso), in termini di aumento del coordinamento e della creatività e riduzione della complessità e del time-to-market.
Il concetto è che l’azienda ha avviato un cambiamento culturale che consente di rinforzare la componente industriale della supply chain, e gli indici tipici di Qualità,
Produttività e OnTime Delivery, con una componente di miglioramento della creatività che è fondamentale in un settore come il fashion.
«La creatività non si può suscitare girando un interruttore – scrive Imai – ma kaizen può aiutare a eliminare i fattori di disturbo affinché gli operatori possano concentrarsi su quello che sanno fare meglio».