Garantire la sicurezza sul lavoro è un’attività che non conosce pause e non permette distrazioni né incompetenza: lo sa bene il Datore di lavoro 4.0, chiamato a fronteggiare un cambiamento epocale nel mondo del lavoro, frutto della digitalizzazione e del rapido progresso tecnologico.
Quale soggetto titolare del potere di organizzare, gestire, dirigere e controllare i lavoratori, il Datore di lavoro è da sempre tenuto a raggiungere gli obiettivi aziendali garantendo la tutela, l’incolumità e il benessere psicofisico del lavoratore (Health & Safety), al contempo salvaguardando la posizione dei lavoratori da eventi legati ad atti lato sensu criminali (Security). Ma cosa cambia nel panorama della Quarta Rivoluzione industriale e come si evolve il ruolo del Datore di lavoro 4.0?
Il tema è stato recentemente affrontato dall’Agenzia Europea per la salute e la sicurezza sul lavoro (EU-OSHA), nella ricerca “Foresight on new and emerging occupational safety and health risks associated with digitalisation by 2025” pubblicata a conclusione di uno studio biennale sugli effetti della digitalizzazione sulla sicurezza e la salute sul lavoro (SSL) nell’UE.
L’EU-OHSA ha elaborato un’analisi previsionale secondo la quale il futuro potrà evolvere seguendo due principali linee direttrici:
- automazione, complessità e interconnessione dei processi di lavoro;
- autonomia nell’organizzazione del lavoro, autoapprendimento e autogestione.
Molte attività lavorative saranno svolte direttamente attraverso processi di automazione e i lavori che non saranno attuati direttamente dalle Macchine richiederanno comunque un elevato grado di interazione Uomo-Macchina, il che comporterà la necessità di sviluppare competenze digitali che oggi i lavoratori non possiedono.
Il Datore di lavoro 4.0 dovrà quindi poter contare su figure professionali in grado di manifestare una certa attitudine al digitale e un set di digital skill.
Tra gli attori principali, nell’ambito della tutela della salute e sicurezza, vi saranno le risorse dedicate alla manutenzione degli impianti “intelligenti”, governati dall’Internet of Things, dalla Robotica e dall’Intelligenza Artificiale, che rappresentano i principali strumenti per realizzare la digital transformation in sicurezza.
Il ruolo dell’IoT e la manutenzione predittiva
«Accanto alle tradizionali forme di manutenzione ordinaria e straordinaria, oggi, grazie all’IoT, sta assumendo sempre maggiore rilievo la cosiddetta manutenzione predittiva. Essa, sulla base dell’analisi dei dati di una macchina e di quelle che – in gergo tecnico – sono definite “root case analysis”, é in grado di determinare quando gli interventi manutentivi devono essere effettuati per prevenire non solo rotture o fermi produttivi, ma anche incidenti o infortuni sul lavoro», spiega Andrea Berni, Manager Practice QHSE di P4I – Partners4Innovation.
Who's Who
Andrea Berni
Manager Practice QHSE, P4I - Partners4Innovation
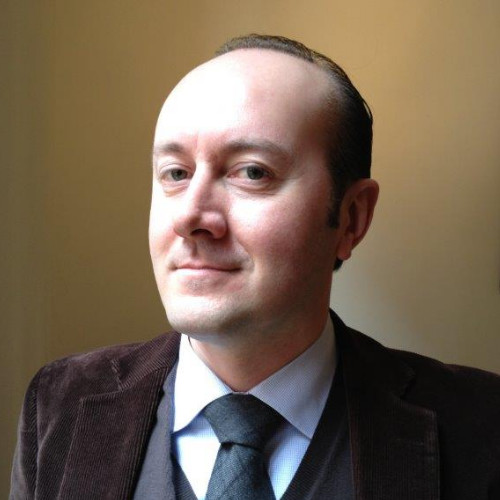
L’IoT, infatti, consente di controllare ogni singola macchina connessa a un sistema e di avere a disposizione, in tempo reale, una mole di dati e di informazioni tali da riuscire ad anticipare la manutenzione in funzione del tempo, dei cicli di produzione e della modalità di utilizzo dell’impianto stesso, a prescindere dalle indicazioni del produttore.
Le tecnologie IoT applicate all’industria, quindi, se da un lato fungono da strumento di controllo per il miglioramento del processo produttivo, aumentando produttività ed efficienza, dall’altro rappresentano una nuova chance per le aziende, in grado di migliorare le misure di salute e sicurezza sul lavoro, soprattutto negli ambiti lavorativi più esposti al rischio, rendendo più agevole l’assolvimento degli obblighi di cui al D.lgs. n. 81/2008 e prevenendo gli incidenti sul lavoro.
«É ormai dimostrato che quando la manutenzione predittiva viene eseguita in modo sistematico, oltre a ridurre al minimo i tempi di fermo di una macchina, con conseguente aumento della capacità produttiva di un impianto, può scongiurare gli infortuni sul lavoro, spesso causati da errori di programmazione e di investimento degli interventi manutentivi e di revamping degli impianti. Con la Manutenzione 4.0, dunque, si riesce ad intervenire prima che si realizzi un guasto o si verifichi un potenziale incidente in danno degli stessi lavoratori», continua Berni.
I lavoratori 4.0, inoltre, dovranno sapere interagire con i nuovi DPI (Dispositivi di Protezione Individuale), muniti di sensori IoT, in grado di inviare messaggi di allarme istantanei, in caso di pericolo, anticipando fughe di gas, incendi ed esplosioni, o allertando del pericolo di un malore o di un incidente.
Migliorare i livelli di salute e sicurezza…con la tecnologia: alcuni esempi
Alcune aziende, al fine di accrescere i livelli di salute e sicurezza, hanno sviluppato appositamente dei dispositivi wearable intelligenti (braccialetti) in grado di monitorare la frequenza cardiaca dei dipendenti e ridurre sensibilmente i rischi connessi a possibili casi d’infarto durante i turni lavorativi. Altre aziende hanno realizzato dei berretti e caschi da lavoro che tengono sotto costante controllo le onde cerebrali dei lavoratori, interpretano il loro stato emotivo e determinano l’adeguatezza della frequenza e della durata dei periodi di pausa, riducendo o quantomeno contenendo entro i limiti di guardia l’eventuale stress psico-fisico connesso alle prestazioni di lavoro.
Altre realtà utilizzano piattaforme IoT, costruite tramite la mappatura degli interni degli stabilimenti e l’impiego di una rete di sensori che comunicano con i wearable indossati dai lavoratori, che si attivano solamente in caso di emergenza, in modo da gestire il soccorso del lavoratore nel migliore dei modi e senza infrangere la sua privacy.
«Tutto questo rappresenta un vero successo, in ambito di salute e sicurezza sul lavoro. Al contempo, però, il digitale apre la porta ad un pericolo nuovo e incombente per i lavoratori – ricorda Berni- e cioè il rilevante rischio di attacchi cyber verso gli impianti IIoT (Industrial Internet of Things) o i dispositivi IoT, sempre più soggetti a crimini con finalità di cyber spionaggio e cyber sabotaggio. Ecco perché per il Datore di lavoro 4.0 non può esimersi dal rilevare il cosiddetto ‘rischio informatico’ applicato alle Macchine».
Cyber attacchi e tutela dei lavoratori
Cosa fare per la tutela dei lavoratori, in caso di attacchi informatici nei processi produttivi, sempre più governati dalla Macchina? Quali sono le misure di recovery per la sicurezza fisica in caso di disattivazione dei dispositivi di sicurezza della macchina a seguito di cyber attack?
«Sono proprio questi i temi che la Sicurezza 4.0 dovrà affrontare – aggiunge Berni -. Nel momento in cui la Robotica e l’Informatica si integrano alla Produzione Industriale su amplia scala è inevitabile che le problematiche di un mondo cyber, apparentemente virtuale, si vadano ad estendere anche al mondo fisico industriale. La cultura dell’analisi-valutazione e prevenzione dei rischi fisici nelle aziende, con un po’ di fatica e con qualche forzatura burocratica, alla fine si è diffusa. Meno diffusa, se non totalmente assente, è l’analisi integrata del rischio informatico in ambito industriale, associato al rischio fisico».
Anche dal punto di vista normativo, questi temi non sono trattati. Non sono affrontati da leggi, e neppure da direttive europee o norme tecniche. Un esempio per tutti è la Direttiva Macchine (DIR 2006/42 CE), che si preoccupa di far compiere una valutazione dei rischi al fabbricante della macchina in relazione all’uso previsto della macchina, o all’uso scorretto ma ragionevolmente prevedibile, mentre non dice nulla rispetto alle misure di prevenzione che la macchina deve adottare in seguito ad un attacco informatico (che è certamente da intendere come una esplicita e dolosa violazione di una regola). «Come conseguenza di ciò, nella maggioranza dei casi, il costruttore non tiene conto degli effetti della IT-Security sulla sicurezza fisica. E, mutatis mutandi, succede lo stesso per quanto riguarda il rischio sul luogo di lavoro: non è prassi che tali aspetti vengano contemplati nei D.V.R. (Documenti di Valutazione dei Rischi) a cura del Datore di lavoro 4.0».
Per fortuna si stanno vedendo segnali di cambiamento, quanto meno in ambito internazionale, sia nel mondo ISO, che nel campo IEC. «In ambito ISO, si sta sviluppando un rapporto tecnico, mentre in ambito IEC una norma, ed entrambe le soluzioni andranno ad indicare i requisiti che i fabbricanti di macchine dovranno rispettare per fare in modo che le loro Macchine siano, per quanto possibile, sicure dagli attacchi informatici», conclude Berni.
D’altra parte, come la produzione non è più appannaggio esclusivo degli operai, ma dei Lavoratori 4.0, così la Sicurezza del lavoratore, oggi, dipende irrimediabilmente dalla Cyber-Security.