Si chiama Industria 4.0 il nuovo orizzonte di una produzione e di una distribuzione che diventano più smart, vale a dire più intelligenti, più veloci e più efficienti. In che modo?
Grazie a un mix tecnologico di automazione, informazione, connessione e programmazione che sta portando a un cambio dei paradigmi tecnologici e culturali. Questo cambio coinvolge il sistema manifatturiero in tutte le sue forme, introduce nuovi concept di sviluppo e di servizio all’insegna di una digital trasformation sempre più spesso sinonimo di disruption.
Il suffisso 4.0, infatti, corrisponde alle tappe di un’evoluzione estremamente precisa. Dall’introduzione della macchina a vapore all’uso sempre più pervasivo dell’automazione, dall’informatizzazione alla digitalizzazione. Il passaggio alla quarta rivoluzione industriale traghetta le imprese verso una nuova dimensione detta bimodale, perché costituita da un ecosistema di risorse fisiche e virtuali.
Figlia di quella digital transformation che sta progressivamente cambiando usi e costumi, innescando una rivoluzione culturale su scala globale, l’Industria 4.0 in questi ultimi anni è diventata anche una nuova dimensione della comunicazione e del business.
Indice degli argomenti
Industria 4.0: storia ed evoluzione tecnologica
Nell’infografica sottostante ecco la road map che riassume le 4 tappe evolutive della storia industriale.
1784 – Industria 1.0
L’Industria 1.0 corrisponde a una rivoluzione della manifattura rispetto all’uso dell’energia. L’invenzione della macchina a vapore, infatti, consente alle fabbriche di abbandonare mulini e introdurre una meccanizzazione della produzione all’insegna di una maggiore velocità e potenza.
1870 – Industria 2.0
L’Industria 2.0 rappresenta la seconda generazione energetica, legata all’utilizzo dell’elettricità prima e del petrolio poi, che permettono di incrementare ulteriormente i livelli di meccanizzazione e di produzione. È grazie a questa rinnovata potenza che nella manifattura si afferma progressivamente quella catena di montaggio che inaugura l’era della produzione di massa.
1970 – Industria 3.0
L’industria 3.0 riassume l’ingresso in fabbrica dell’ICT di prima generazione. Informatica ed elettronica incrementano ulteriormente i livelli di automazione non solo nell’ambito produttivo, ma anche (e soprattutto) organizzativo. Si diversificano le infrastrutture e si avviano nuovi processi che, all’insegna della progressiva digitalizzazione, differenziano e agevolano il lavoro delle persone migliorando la qualità della produzione.
2011 (e oltre) – Industria 4.0
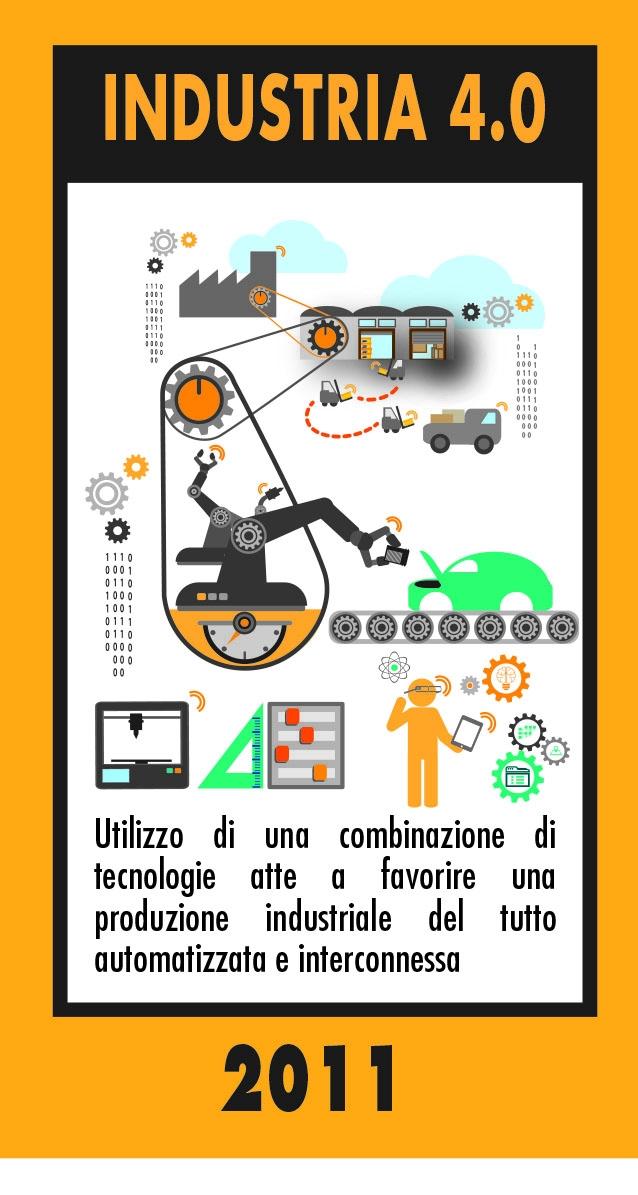
L’Industria 4.0, includendo un mix tecnologico di robotica, sensoristica, connessione e programmazione, rappresenta una nuova rivoluzione rispetto al modo di fabbricare i prodotti e di organizzare il lavoro. Come? Grazie a nuovi modelli di produzione sempre più automatizzati e interconnessi, asset e prodotti intelligenti e comunicanti, una tracciabilità e una rintracciabilità dei processi. Queste ultime conducono a una gestione delle informazioni collettiva, condivisa e collaborativa a livello di filiera, nuove logiche di servizio all’insegna del cloud e della mobility.
Nasce una Internet di ultima generazione, Industrial Internet, capace di portare dentro e fuori dalle fabbriche più informazione, più integrazione, più interazione e più efficienza. Si rinnovano i processi e i sistemi, ma anche nuove regole di comunicazione e di servizio. Software di nuova generazione da un lato e Big Data Management dall’altro: è così che la produzione riesce ad arrivare a una personalizzazione di massa. La continua evoluzione delle tecnologie sta diversificando la declinazione del 4.0 su più livelli e ambiti operativi associati all’uso dell’Intelligenza Artificiale e di tutte le evoluzioni del digitale, Blockchain inclusa.
Da dove nasce il termine Industria 4.0
Termine di nuovo conio che ha dato l’abbrivio a una reinterpretazione della nostra cronistoria tecnologica, Industria 4.0 è stato usato per la prima volta nel 2011 alla Fiera di Hannover, in Germania. Da un’ipotesi progettuale ha preso le mosse un gruppo di lavoro che nel 2012 ha presentato al governo federale tedesco una serie di raccomandazioni per l’implementazione del Piano Industria 4.0. L’8 aprile 2013, sempre alla Fiera di Hannover, è stato diffuso il report finale con una previsione degli investimenti necessari su infrastrutture, scuole, sistemi energetici, enti di ricerca e aziende. Il modello doveva servire ad ammodernare il sistema produttivo tedesco e riportare la sua manifattura ai vertici mondiali, rendendola competitiva a livello globale. Dalla Germania, poi, è stato fonte di ispirazione per tutti gli altri Paesi.
I dati dell’industria 4.0 in Italia
Stando all’ultimo report realizzato dall’Osservatorio Transizione Industria 4.0 del Polimi, in Italia nel 2020 il volume d’affari ha raggiunto i 4,1 miliardi di euro, con una crescita dell’8% rispetto all’anno precedente. Un risultato certamente positivo, sebbene la crescita del mercato sia stata inferiore alle previsioni formulate nel 2019 (+20%) se si considera che le stime effettuate durante il primo lockdown delineavano un calo del 5%. A fare da buster per l’utilizzo delle nuove tecnologie nel settore industriale smart working, impegno verso la sostenibilità e agevolazioni fiscali. Così sono circa 1.400 le applicazioni di Industria 4.0 utilizzate dalle imprese manifatturiere, il 28% in più rispetto al 2019.
Le più diffuse sono le soluzioni di Industrial IoT, pari a un quarto del totale (380, +31%), spesso combinate con algoritmi di Analytics e Intelligenza Artificiale. Seguono le tecnologie Advanced HMI, come i wearable e le interfacce uomo-macchina per acquisire e veicolare dati in formato visuale, vocale e tattile (286, +15%). Inoltre, Advanced Automation (241, +5%), cioè i sistemi di produzione automatizzati come i robot collaborativi, e Industrial Analytics. Queste sono le applicazioni più in crescita (200, +39%), focalizzate sulla previsione delle prestazioni degli assetti industriali e dei processi produttivi. Infine, a chiudere l’elenco le applicazioni di Cloud Manufacturing (140, +33%), utilizzate soprattutto per il monitoraggio e la diagnostica degli impianti industriali da remoto, e quelle di Additive Manufacturing (125, +30%).
Smart manufacturing, un trend in crescita
Che la tendenza positiva non si è arrestata nemmeno durante la crisi scatenata dal dilagare del Covid-19 lo confermano anche i risultati dello studio rilasciato da Deloitte, L’importanza di un approccio ecosistemico alle iniziative di industry 4.0. Una fotografia del settore manifatturiero italiano. Dallo studio di rileva come durante la pandemia, malgrado la battuta d’arresto che abbia investito tutta l’economia, il 63% delle aziende manifatturiere italiane prese in esame non solo non ha interrotto i flussi di capitali a supporto dei progetti di produzione intelligente, ma li stia accelerando con una media di più di un terzo del proprio “factory budget”.
Tuttavia, se da un lato le aziende italiane si confermano molto ricettive rispetto alle singole iniziative di smart manufacturing, scalare tali iniziative è spesso complesso. Infatti, solo il 27% del campione è riuscito a superare la trappola della fase pilota, mentre il restante 73% continua a condurre tali progetti con una logica sperimentale di tipo “spot”, che non va oltre le mura dell’impianto produttivo.
Incentivi e agevolazioni per industria 4.0
Dopo il Piano Nazionale Industria 4.0 – 2017-2020, presentato nel settembre 2016 dal Ministro dello Sviluppo Economico Carlo Calenda, che prevedeva un insieme di misure organiche e complementari in grado di favorire gli investimenti per l’innovazione e la competitività, il Mise (oggi ministero delle Imprese e del Made in Italy) ha dato vita al Piano Transizione 4.0. Potendo contare sulle risorse stanziate dalla Legge di Bilancio collegata al PNRR (pari ad oltre 24 miliardi di euro per il biennio 2021-2022), il Piano Transizione 4.0 ha incentivato l’innovazione e l’Industria 4.0 concedendo agevolazioni fiscali in forma di credito d’imposta sugli investimenti effettuati dalle imprese in beni materiali e immateriali da utilizzare esclusivamente in compensazione.
Il cambiamento delle aliquote nel 2023
A partire dal 2023 sono stati ridotti sensibilmente i benefici e, nel caso del credito d’imposta per la Formazione 4.0, sono stati azzerati. In sostanza, per i beni materiali 4.0 si è passati dall’aliquota del 40% al 20% (fino a 2,5 milioni di euro). Per i beni immateriali 4.0, dal 20% al 10% (per gli importi compresi tra i 2,5 a 10 milioni di euro) e dal 10% al 5% (per gli importi tra 10 a 20 milioni di euro).
La legge di Bilancio 2023 è intervenuta solo per posticipare da giugno a settembre la scadenza per la consegna dei beni materiali 4.0, a patto che gli ordini effettuati entro il 31 dicembre 2022 siano stati confermati con il versamento di un acconto pari ad almeno al 20%. La scadenza, poi, è stata ulteriormente posticipata al 31 dicembre 2023 dal decreto Milleproroghe convertito nella Legge 24 febbraio 2023, n. 14.
In ogni caso, la partita delle aliquote non è ancora chiusa. Il ministro delle Imprese e del Made in Italy, Adolfo Urso, si è pronunciato in più di una occasione per riportarle al livello precedente, ma per farlo bisognerà attingere alle risorse del PNRR.
Tecnologie abilitanti dell’industria 4.0
Progressi tecnologici e produttività industriale hanno avuto sempre un profondo legame, e non potrebbe essere diversamente oggi. Le nuove tecnologie stanno modificando in maniera dirompente le nostre abitudini quotidiane, dalla formazione scolastica allo shopping, ma anche il settore il settore produttivo. Tra le molteplici innovazioni dell’ultimo periodo, le tecnologie abilitanti dell’industria 4.0 sono nove, molte delle quali già in uso, ma oggi interconnesse tra loro e per questo in grado di generare un flusso di produzione perfettamente integrato. Nello specifico, le tecnologie sono:
- Big Data Analytics;
- Robot autonomi;
- sistemi di simulazione come per esempio la simulazione 3D;
- integrazione orizzontale e verticale tra tutti i sistemi del processo produttivo;
- tecnologia IoT applicata ai macchinari;
- Cybersecurity;
- Cloud Computing;
- Realtà Aumentata;
- Additive Manufacturing, cioè sistemi di produzione additiva che aumentano l’efficienza dell’uso dei materiali partendo dalla stampa 3D.
A sua volta, l’Osservatorio Industria 4.0 del Politecnico di Milano dà una sua classificazione delle tecnologie abilitanti dell’industria 4.0, che individua in sei tipologie, dividendole in due macro-categorie: una più vicina all’IT, della quale fanno parte Internet of Things, Big Data e Cloud Computing; l’altra, più eterogenea e vicina al livello operativo, formata da Advanced automation, Advanced HMI (Human Machine Interface) e Additive Manufacturing.
Industria 4.0, smart fabric o smart manufacturing?
Le soluzioni coinvolte sono quindi tantissime. Organizzarle in maniera armonica e coordinata è una sfida che ha bisogno di competenze diversificate e di vision ampie e lungimiranti. Il denominatore comune? Un’integrazione dei processi e delle procedure che coinvolge tutte le filiere, traghettando così le imprese verso nuovi modelli di sviluppo della produzione e del business, diversificati e complessi.
Gli esperti di Boston Consulting o McKinsey parlano di smart fabric, proponendo una ripartizione dei cluster tecnologici su tre livelli:
- SMART PRODUCTION: Nuove tecnologie produttive creano interazione tra tutti gli asset legati alla produzione, favorendo la collaborazione tra uomini, macchine e sistemi.
- SMART SERVICES: Una governance di nuova generazione delle infrastrutture informatiche e tecniche aiuta a gestire e presidiare i sistemi, sfruttando logiche di massima integrazione tra tutti gli attori della supply chain, clienti inclusi.
- SMART ENERGY: Nuovi sistemi di alimentazione e un’attenzione al monitoraggio dei consumi energetici che rendono le infrastrutture più performanti, più economiche e più ecologiche.
L’innovazione tecnologica, infatti, migliora e rende più efficiente da un lato i processi di produzione, dall’altro i processi di gestione.
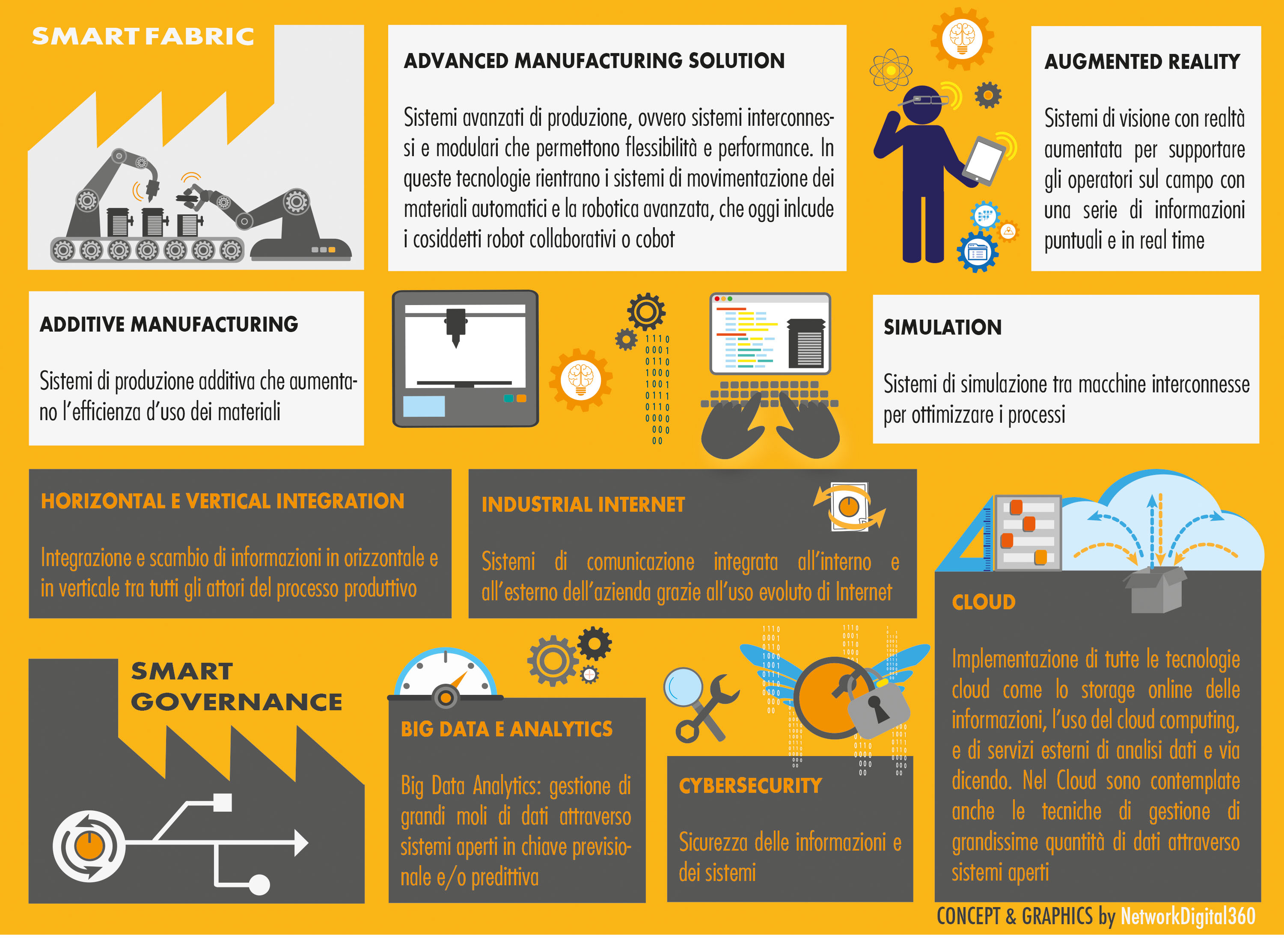
Il manufacturing nell’era delle smart tecnologies
Gli analisti dell’Osservatorio Industria 4.0 del Politecnico di Milano entrano ancora più nel dettaglio, analizzando tutte le smart technologies del manufacturing. Dal loro punto di vista, smart manufacturing non significa adottare in modo isolato questa o quella tecnologia innovativa, quanto piuttosto mettere a fuoco il meccanismo complessivo attraverso cui la maggiore integrazione delle risorse genera del valore addizionale. Significa, quindi, ridurre le inefficienze, valorizzare la conoscenza e migliorare la capacità di pianificare e reagire.
Ne deriva una schematizzazione dei tre ambiti in cui le tecnologie digitali stanno cambiando modelli e approcci nell’ambito dello smart manufacturing:
- SMART LIFECYCLE MANAGEMENT: Comprende l’intero processo di sviluppo di ogni nuovo prodotto, includendo la gestione dell’intero suo ciclo di vita.
- SMART SUPPLY CHAIN: Include la pianificazione dei flussi fisici e finanziari nel sistema logistico-produttivo allargato a tutta la filiera.
- SMART FACTORY: Abbraccia l’intera governance legata a infrastrutture e servizi, tra cui produzione, logistica interna ed esterna, manutenzione, qualità, sicurezza e rispetto delle normative.
Nel futuro immaginato dallo smart manufacturing, dunque, gli impianti, i lavoratori, i materiali in input e i prodotti finiti saranno dotati di sensori che li identificano e ne rilevano costantemente posizione, stato e attività. A loro volta i dati raccolti saranno analizzati per migliorare la capacità produttiva, l’efficienza, la sicurezza e la continuità operativa. Infine, tutta la fabbrica sarà connessa al resto del sistema logistico-produttivo e ai clienti tramite piattaforme cloud.
Articolo originariamente pubblicato il 18 Ott 2021