L’innovazione digitale e l’automazione premiano Mebra Plastik, azienda di Varese che produce tubi per l’oleodinamica e la pneumatica. Un processo di trasformazione avviato già da cinque anni ma che ha permesso ora di sostenere l’impatto della pandemia.
Mebra Plastik ha sofferto come molte altre imprese di un drastico calo della domanda durante il primo lockdown. In autunno, però, è tornata la crescita, con un’impennata di ordini. L’azienda ha dovuto gestire il boom di domanda con un numero di dipendenti ridotto del 75%, tra quarantene fiduciarie e una decina di colleghi risultati positivi al tampone eseguito in azienda sui 108 dipendenti (di cui un’ottantina in produzione e magazzino).
Linee automatizzate e magazzino ben fornito
L’azienda lavora già su tre turni e utilizza da tempo macchine automatiche che, negli ultimi due anni, sono state collegate a un MES per il controllo della produzione. Il sistema raccoglie i dati sull’andamento delle macchine, li collega al gestionale aziendale e pianifica e ottimizza la produzione in base agli ordini e al rendimento. La minore presenza di personale con ruolo di supervisione e di calibratura dell’avviamento delle macchine ha portato a concentrare la produzione sulle linee di ultima generazione, che hanno una produttività più alta (con velocità anche tripla) e consumi inferiori.
«Abbiamo garantito la “tenuta” delle consegne, oltre che negoziando con i nostri clienti (63% in Italia, 37% all’estero) e allungando i cicli delle macchine più performanti, grazie a un magazzino ben rifornito. Questa scelta strategica si sta rivelando utile anche nei periodi di freno della capacità produttiva. Noi facciamo tubi, ma in 35mila varianti, è questo che ci distingue dalla concorrenza. L’offerta è molto differenziata e sono fondamentali sia il magazzino ben fornito che la piattaforma B2B automatizzata, che ora abbiamo arricchito di nuovi filtri per selezionare il prodotto con un potente motore di ricerca. E poi contiamo su un rapido ritorno alla normalità, anche con il contenimento dei contagi», racconta il responsabile delle Operations di Mebra Plastik, Samuele Maugeri, terza generazione della famiglia Metti in azienda.
Who's Who
Samuele Maugeri
Responsabile Operations, Mebra Plastik
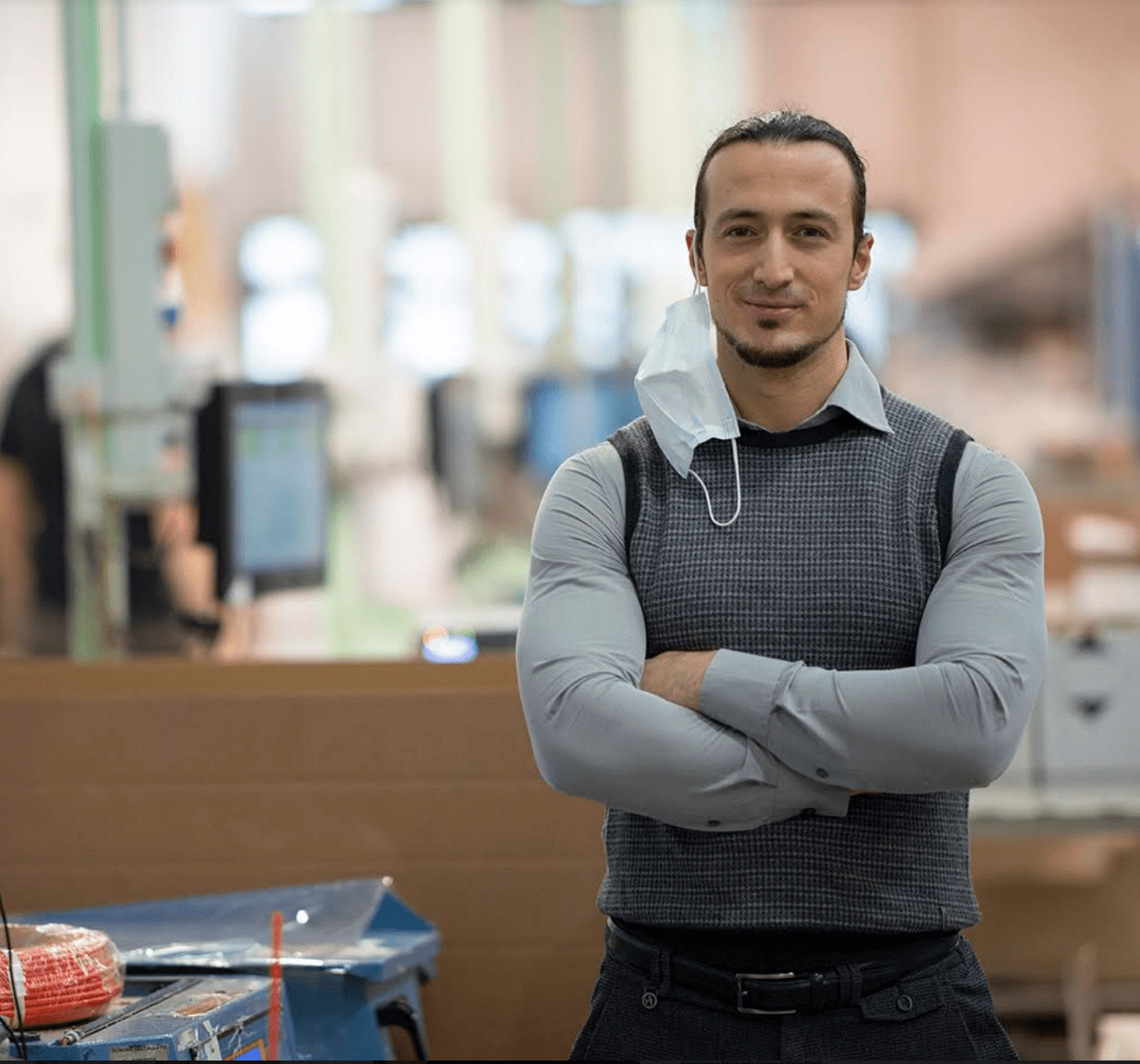
Gli inizi in un garage
L’azienda nasce nei primi anni ’70 grazie allo spirito di iniziativa di Mario Metti. A tre anni dalla pensione in un’azienda del settore delle plastiche, Metti decide di farsi pagare la liquidazione con un estrusore per iniziare a produrre in proprio.
«Mio nonno si sentiva troppo giovane per andare in pensione e, incoraggiato da mia nonna, decise di investire la sua liquidazione in un macchinario», racconta Maugeri. L’azienda cresce velocemente e da quel garage nella zona residenziale di Busto Arsizio si sposta nell’area industriale negli anni ’80. I figli entrano in azienda e contribuiscono al suo sviluppo.
Oggi Mebra Plastik è un’impresa da 19 milioni di euro di fatturato, distribuita su 36mila metri quadri su quattro civici, di cui 18mila coperti tra produzione, magazzino e uffici.
La transizione digitale
La trasformazione digitale è partita cinque anni fa proprio dal magazzino, che è stato organizzato con un software per favorire la logistica e indirizzare i magazzinieri, ciascuno dotato di palmare.
«Dopo le prime naturali resistenze, gli operatori hanno riconosciuto l’utilità dello strumento digitale per velocizzare le operazioni e accelerare l’inserimento di nuove figure. L’inserimento diventa immediato, mentre prima ci volevano sei mesi di formazione», racconta Nicola Marchesin, responsabile IT di Mebra Plastik.
Who's Who
Nicola Marchesin
Responsabile IT, Mebra Plastik
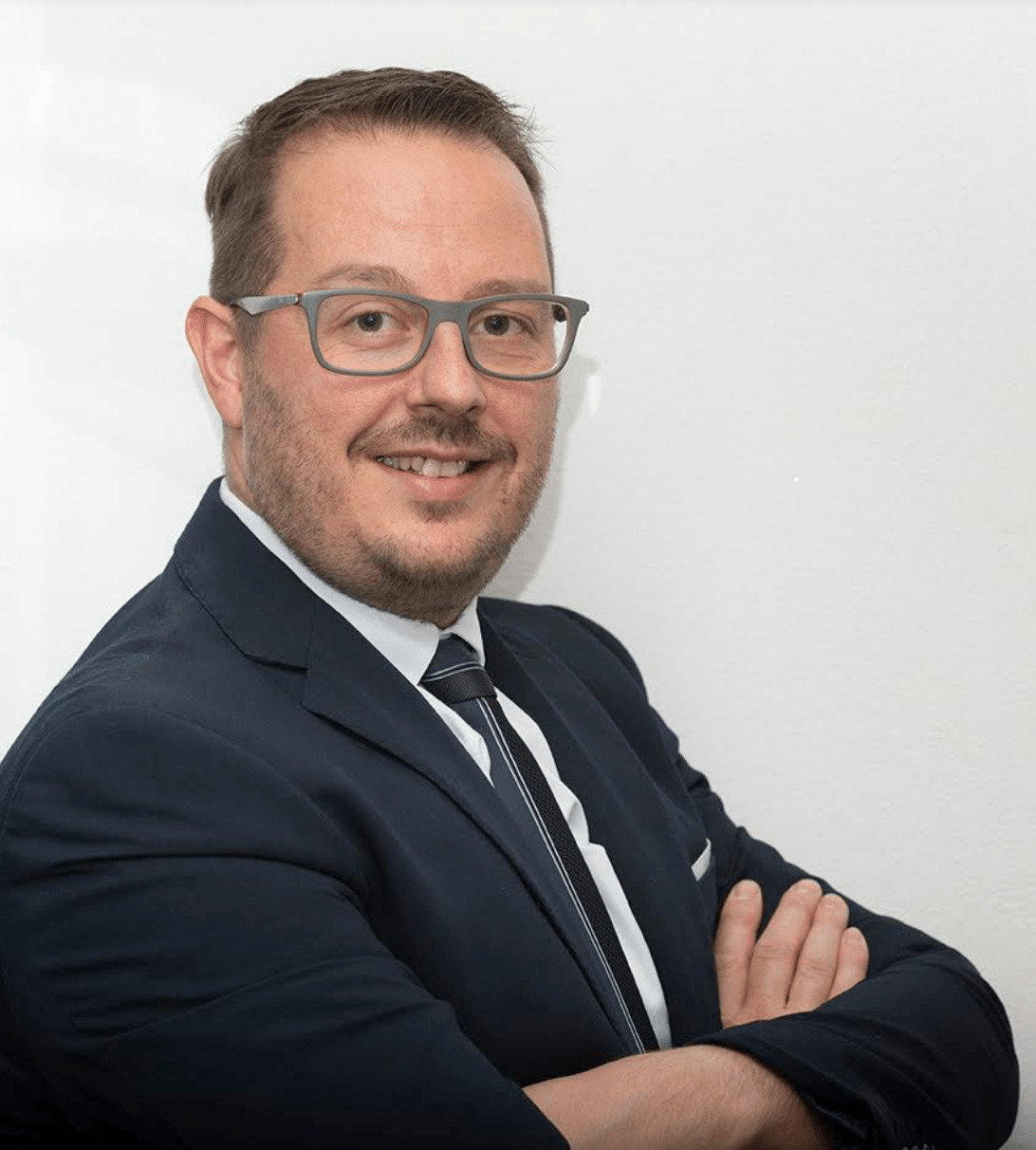
Il prossimo passo sarà l’automatizzazione del magazzino. Il processo è stato interrotto dalla pandemia, ma verrà ripreso appena possibile. Un altro progetto in dirittura d’arrivo è la robotizzazione dell’area assemblaggio con bracci robotici e AGV, veicoli industriali a guida autonoma che prelevano e spostano gli oggetti da fine linea all’area assemblaggio.
La scelta di una produzione non “just in time”
La scelta controcorrente di tenere un magazzino con migliaia di articoli ha permesso di rispondere a due esigenze simultaneamente.
«Da un lato assicurare un’ampia scelta di prodotti, che produciamo in quantitativi superiori alle richieste alimentando il magazzino (10.000 metri quadri)», spiega Maugeri. «Dall’altro contenere i costi del “just in time”, che richiederebbe continue modifiche di programmazione delle macchine». Una scelta che, di questi tempi, ha permesso di compensare, almeno in parte, la riduzione della capacità produttiva.
L’AD Metti: in pandemia «Monitoraggio costante»
Mebra Plastik ha sostenuto un 10% di costi in più rispetto a quelli preventivati a inizio anno per garantire la sicurezza sul luogo di lavoro. Il programma ha incluso sanificazioni periodiche del comparto produttivo, del magazzino e degli uffici. Sono stati potenziati gli interventi di pulizia (con costi triplicati) e messi a disposizione gel sanificanti. L’azienda ha creato paratie e percorsi di movimento e dotato i dipendenti di dispositivi di protezione individuale, ormai standard. A tutto ciò si aggiunge la disponibilità del tampone, cui hanno aderito quasi tutti i presenti in azienda.
«Ripeteremo lo screening al rientro dalla vacanze natalizie per assicurare un monitoraggio costante, per quanto non sia richiesto dai protocolli», dichiara Patrizia Metti, amministratore delegato Mebra Plastik. «Stiamo predisponendo anche il raddoppio degli spogliatoi per garantire i cambi di turno in assoluta sicurezza. Ci distribuiamo su tutti gli spazi aziendali per avere una sola persona per ufficio. E per le funzioni di staff c’è sempre lo smart working».
Who's Who
Patrizia Metti
Amministratore Delegato, Mebra Plastik
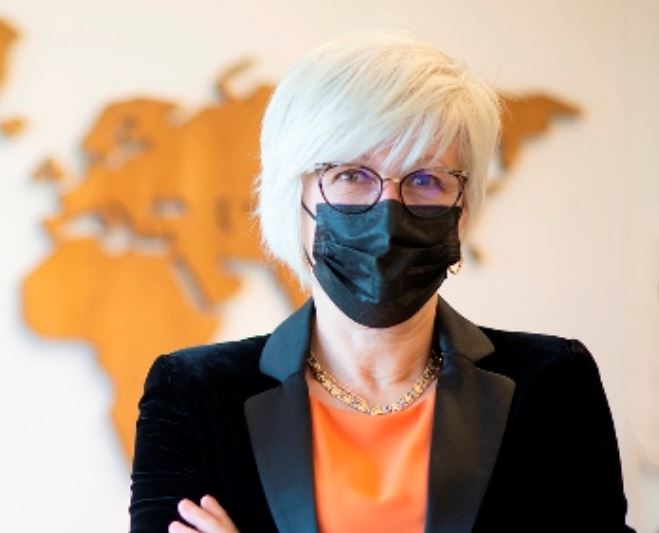