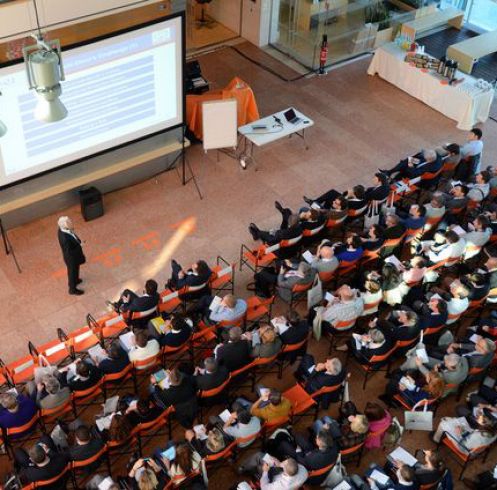
Nel mondo del management, Masaaki Imai è una vera istituzione: è il padre del “kaizen”, termine che in giapponese significa “cambiamento in meglio”, e che lui stesso ha inventato per descrivere l’insieme di metodologie di gestione della qualità che ha portato al successo mondiale le imprese giapponesi negli anni ’70 e ’80, a partire dalla Toyota con il notissimo “Toyota Production System”. Negli anni Imai poi contribuito all’introduzione in molte aziende occidentali di tecniche kaizen come Just-in-time, TQM e TPM, nonché dei principi del Lean Management, con la sua società di consulenza Kaizen Institute.
Ultimamente Imai è stato in Italia, al Muse di Trento, per un evento organizzato dal braccio italiano del Kaizen Institute, dove davanti a 250 imprenditori e manager si è parlato dei principi del kaizen e dei risultati delle aziende trentine che li hanno applicati nell’ambito di un programma sperimentale voluto da Trentino Sviluppo, l’agenzia per lo sviluppo del territorio della Provincia di Trento. In tre anni il programma ha visto l’avvio di dieci cantieri Kaizen, con 25 aziende coinvolte, nei settori meccanico (Luxottica, Dana, e altre), agroalimentare (Filiera Agroalimentare Trentina, Casearia Monti Trentini), funiviario (Funivie Seggiovie San Martino), servizi alla persona (Azienda provinciale per i servizi sanitari di Trento) e, caso unico in Italia, il settore estrattivo, con un cantiere multiaziendale che ha coinvolto una decina di piccole aziende del Distretto del porfido e delle pietre trentine.
In media, le aziende coinvolte hanno registrato aumenti della produttività tra il 10 e il 50%, riduzioni del tempo di attrezzaggio macchine oltre il 50%, del lead time (tempo di attraversamento) fino al 70%, degli spazi occupati dalle linee di produzione fino al 30%, e inoltre cali del 50% dei difetti sul prodotto finito e di oltre il 50% del working capital (scorte e capitale circolante).
C’è sempre un modo migliore per fare le cose, ha spiegato Imai, in un intervento raccontato tra gli altri dal sito VeneziePost. «Il kaizen non è solo miglioramento continuo, e non va confuso con altri concetti, come il Lean Management: troppo spesso le aziende investono in processi “Lean” di trasformazione snella, convinti di ottenere risparmi e semplificazioni istantanei e automatici».
Invece per ottenere risultati solidi occorre un processo condiviso da tutto il personale, esteso a tutte le leve competitive, dalla produzione al marketing e le vendite, e soprattutto continuo, «al contrario dei progetti Lean, che spesso si “spengono”». È impossibile riassumere un insieme di tecniche che è soprattutto un riorientamento dell’intera cultura aziendale al miglioramento continuo e graduale, ma Imai ha provato a “distillare” cinque regole per il kaizen, che ha esposto a Trento.
Il kaizen sintetizzato in cinque regole
La prima è non pensare di poter contare su soluzioni “copia e incolla”. «Non ci sono ricette “chiavi in mano”: il kaizen è un percorso a lungo termine che richiede di cambiare il “sistema operativo” dell’azienda». La seconda è la necessità di coinvolgimento totale del top management. L’introduzione dell’approccio kaizen, sottolinea il guru giapponese, non può essere delegato al middle management aziendale: l’imprenditore e i manager di massimo livello devono partecipare e anzi essere motivatori del percorso verso il miglioramento continuo.
La terza regola è dare responsabilità a tutti i livelli aziendali, in particolare i più bassi, quelli impegnati sul “campo”, a contatto diretto con i clienti, dai quali non raramente arrivano i migliori suggerimenti per migliorare. In un “Cantiere Kaizen” infatti tutti i componenti di uno dei reparti o funzioni aziendali, dal top management agli operai, sono coinvolti nella messa a fuoco di una criticità o una sfida (tempi di produzione troppo lunghi, difettosità dei prodotti troppo alte, sviluppo di un nuovo prodotto) e, guidati in un percorso strutturato in progressiva autonomia, trovano la strada migliore per risolverla.
La quarta è non credere che il kaizen sia alla portata solo delle grandi aziende. «Non è un insieme di modelli per colossi aziendali che vanno “adattati” alle PMI: queste tecniche in realtà sono perfette per le piccole realtà, perché non richiedono grandi investimenti e si basano sul principio che l’energia viene dal basso; poi ovviamente è più semplice coordinare il lavoro in una struttura in cui tutte le realtà aziendali si possono sedere attorno a un tavolo, e quindi è molto più flessibile e si presta naturalmente al rapido allineamento di tutte le sue parti».
E infine l’ultima regola, particolarmente significativa in quest’epoca: puntate meno sulla ristrutturazione finanziaria, dice Imai, e più sulla riorganizzazione operativa. «Rimettete al centro quello che un’azienda sa fare, il know how interno, le eccellenze produttive: in un periodo di crisi l’introduzione del kaizen è ancora più indicata perché non richiede grandi investimenti. Quando la situazione diventa critica molte aziende scelgono una soluzione finanziaria, mentre intervenire sulle attività operative è molto più importante».
Luxottica, tempi di produzione di un occhiale da 26 a 11 giorni
L’evento di Trento ha visto inoltre una rassegna di diversi casi di aziende della zona coinvolte nel programma sperimentale di Trentino Sviluppo. Tra i casi citati c’è per esempio la fabbrica di Luxottica di Rovereto, che ha ridotto il tempo di produzione di un paio di occhiali completo da 26 a 11 giorni, ha recuperato il 30% degli spazi e ha abbattuto del 70% gli interventi di riparazione sulle lavorazioni.
L’azienda Filiera Agroalimentare Trentina Spa ha recuperato il 37% di tempo/lavoro, grazie a un nuovo modello di gestione della produzione che ha riaffidato ai lavoratori la programmazione delle attività, prima definite da un software. Infine Tama, azienda che produce unità filtranti e componenti per impianti di depurazione dell’aria, ha tagliato del 70% il tempo complessivo di produzione, e ha ridotto del 50% il valore del magazzino grazie alla revisione del sistema di riordino.
Visti i risultati della sperimentazione, la Provincia di Trento ha deciso di sostenere le aziende del territorio che applicheranno i metodi kaizen con un contributo medio intorno al 40% della spesa affrontata, come previsto dalla legge provinciale 17/93 che agevola l’acquisizione di conoscenze nelle imprese.